Particle Counter Total Cost of Ownership
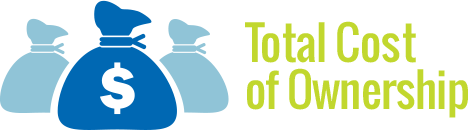
The TCO (Total Cost of Ownership) is a management accounting concept that provides a financial estimate intended to help buyers and owners determine both the direct and indirect costs of a product over its estimated life.
Purchase Price
Several factors affect TCO, and the initial purchase price for a particle counter or microbial sampler is frequently not the #1 cost driver. Today, most corporate buyers are savvy and astute enough to realize that buying based on purchase price alone is an unwise business practice.
In fact, a common pricing strategy employed by many manufactures both within and outside the industry is to design products to minimize cost over quality, sell their product at a low margin, and once the customer is hooked, charge users higher prices for service and consumables (ink, paper, batteries, etc.). The computer printer market is a perfect example. The replacement cost of a single ink cartridge is approximately 33% to even 50% the price of a brand new printer. Why? Because manufacturer's study consumer behavior and they realize that customers buying printers are generally not tech-savvy and fail to look into other areas that affect TCO. Subsequently, most people who buy a computer printer base their decision on price alone, and fail to consider the cost of consumables (i.e., ink and paper). As a consequence, computer printer manufacturers earn higher profits than what could normally be realized on the product itself.
Cost of Operating
A key component in calculating direct and indirect operating costs is to determine the estimated product life cycle. In regulated industries, environmental monitoring equipment with plastic enclosures are generally decommissioned every five years. This is due to accidental damage such as cracks, scratches, scuffs, etc. Some particle counter models (not Climet), are susceptible to increasing out-of-tolerance rates (10% - 20%) when the instrument exceeds 3 years or more. Subsequently, users frequently replace this equipment every seven years. Climet particle counters can operate efficiently for a decade or more, which gives Climet a district advantage in this category.
Users should review their preventative maintenance plans with regards to the frequency and cost of battery replacements and thermal paper usage. Batteries are generally replaced on portable particle counters and microbial samplers every 3-5 years. Some of these manufacturers require users to send their instrumentation back to the factory for battery replacements, at which time a calibration is also charged. This turns a relatively inexpensive service issue into an expensive factory service averaging over $600 to $800.
The frequency of the interval calibration, and its cost should be calculated over the estimated life of the instrument.
Users must also determine the hidden or indirect cost of being out-of-tolerance on an interval calibration. In regulated industries, an out-of-tolerance calibration will necessitate a deviation report and failure investigation, which has an average cost of $8,000 - $12,000 for even a simple failure investigation. This is almost all labor, involves multiple people and departments, and is difficult to calculate. For example, if you have 100 particle counters, and we have historically experienced a 10% out-of-tolerance rate, with an average cost of $10,000, then we can conservatively budget $100,000 per year for Cost of Poor Quality (CoPQ). Using the same example, but a 2% out-of-tolerance rate, we can conservatively budget $20,000/year. If we then multiply these figures by a 10 year life expectancy, then we can easily see that even a small reduction in out-of-tolerance rates may have a HUGE impact on TCO.
Replacement Cost is frequently calculated in order to normalize a comparison of two instruments that have different estimated life cycles. For example, if you compare a product that is expected to last 5 years against a product that is expected to last 10 years - then we must double our acquisition costs and associated labor.
Cost of Not Operating
The third and final part of the TCO equation is, "The cost of not using." This can be particularly important for continuous process industries, where production occurs on a daily basis. When equipment fails due to a component or workmanship defect, or if the instrument must be returned to the factory for normal maintenance (such as a battery replacement), there is cost involved. This generally involves having to procure additional spares to ensure operations are not shut down unnecessarily. Additionally, there are labor and other costs associated with shipping the instrumentation back to the factory, as well as receiving the product.
Limitations of TCO
Strictly using TCO as a means for making a purchase decision does have its shortcomings. When used with measurement instrumentation, for example, TCO does not measure the accuracy and stability of measurement, which together are of utmost importance in both metrology and quality terms. Additionally, in regulated industries, especially when public health is at risk, it is difficult to put a monetary value on abstract qualities such as trust and assurance. For many Climet customers, this is the exclusive reason that Climet instrumentation is sole sourced throughout their production facilities.
Another example might be convenience. For example, Climet offers customer onsite calibration, whereas this service may not be available with other manufacturers.
Climet urges customers and prospective customers to fully evaluate their alternatives, and not simply choose a solution based on purchase price alone! Climet competes based on Total Cost of Ownership, quality assurance (accuracy and stability of measurement), and superior service.